Perovskite Solar Cells with Self Assembled Monolayers
Overview
This technology describes a novel approach to improving the mechanical reliability and performance of perovskite solar cells (PSCs) through the use of halide-terminated self-assembled monolayers (halide-SAMs) as molecular "glue" between different layers of the solar cell. The innovation focuses on using these SAMs, particularly iodine-terminated SAMs (I-SAMs), to strengthen the typically weak interfaces between the metal halide perovskite (MHP) layer and both the electron transport layer (ETL) and hole transport layer (HTL), resulting in better mechanical stability and improved overall performance.
Market Opportunity
The technology addresses a critical challenge in the commercialization of perovskite solar cells, which are promising for their low cost and high efficiency but have been held back by stability issues. In 2023, the global solar energy market was estimated at $253.69 billion and is expected to grow with a CAGR of 6% to reach $436.36 billion by 2032. North America was the dominant segment in the solar power industry at a 41.30% market share in 2023, and the US solar power market is expected to grow. With increasing demand for more efficient, durable, and cost-effective solar solutions, this innovation could help accelerate the adoption of PSCs in traditional solar panels and emerging applications like building-integrated photovoltaics. The solution-processing approach at room temperature makes it particularly attractive for large-scale manufacturing, potentially enabling wider commercial adoption of perovskite solar cells.
Innovation and Meaningful Advantages
The key innovation lies in the unique molecular design of the halide-SAM, which creates strong coordination bonds between layers while simultaneously reducing defects at the interfaces. The approach demonstrated remarkable improvements in multiple critical areas.
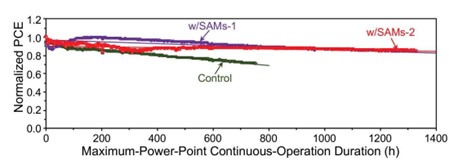
- Novel molecular interface engineering using halide-SAMs that creates stronger bonds between layers while reducing defects, resulting in a 50% increase in adhesion toughness at critical interfaces/
- Significant improvement in operational stability, with projected lifetime T80 increasing by more than 5x (from ~700 to ~4,000 hours)
- Enhanced power conversion efficiency (from 20.2% to 21.4%)
- Reduced hysteresis from 8.8% to 2.9% without requiring complex processing methods
- Room-temperature, solution-based process that's compatible with existing manufacturing methods and scalable for commercial production
Collaboration Opportunity: We are interested in exploring research collaborations and licensing opportunities.
References
Principal Investigator